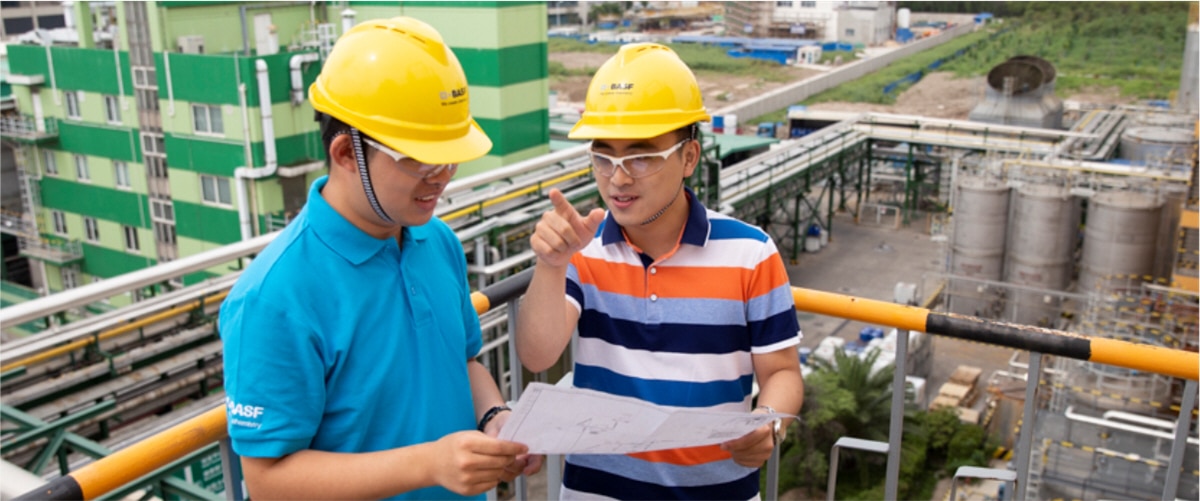
Production Engineer
Objectives of the Position
Ensure to deploy information’s at shopfloor comes from Production Manager and vice a versa. Upkeep the production documentation includes QMS; EMS and RCMS and others. Upkeep the Production database on daily basis in different system includes SAP and others. Ensure to Maintain minimum inventories of all consumable items required in production department. Comply other BASF rules.
Main Areas of Responsibilities and Key Activities
BASF Group Objective, EHS and Statuary Compliance Responsibility:
- Having responsibility as per Emergency response plan.
- Ensure to raise define yellow cards and maintain closing rate as per define KPIs target.
- Responsible for ensuring EHS standards as per BASF Guidelines at plant and understand EHSQ Policy and Objectives etc.
- Taking part in Safety and troubleshooting analysis and taking help to report the same in correct tools for any incident/Accident related to process which should happened in the plant.
- Ensure compliance with HSE Policies and regulations, Prepare and help to release work procedure.
- Assist to Production Manager on TDS and RCMS related activities.
- Report yellow cards as per define targets and help Manager for closing the yellow cards as per target.
RCMS Responsibility:
- Responsible as RC code champion for RC Code 03 i.e., Occupational Safety.
- Responsible to Reporting Manager for the implementation of the EHS Policy and RC.
- Set an example for providing safe working culture and help to arrange infrastructure for safe operation.
- Assist to Production Manager to ensure that employees and contractors are informed of RC requirements.
- Assess employee safety performance and given any additional training requirements as an when required related to plant safety.
- Ensure that all RC rules, procedures, regulations and safe working practices are understood and adhered to by all employees and contractors.
- Assist Production Manager to conduct Periodic inspection of Work Permits at Workplace.
- Perform the role as defined in On-site Emergency Plan to mitigate the emergencies.
- Quality Management:
- Support Production Manager to implement “Quality is beyond productivity” by facilitating required training by means of assisting to identify quality training of team through yearly training plan.
- Create a Quality mind-set. Always strive for superior product quality via continuous improvement and conducting quality sessions on need basis.
- Prepare and update QMS and EMS related Procedures, WIs and Documents as an when required.
- Effective quality corrective/ preventive action &implementation to minimize justified customer complaint and improve the processes.
- Develop a quality mindset in the plant peoples to minimize the internal reject too in parallel to justified customer claim.
- Participate in RCPS session to resolve internal and external quality issues and help to close define action plans.
Budget Control:
- Support Production Manager to Plan, evaluate and develop annual budgets for Operation Improvement activities.
- Create budget related documents to close Capex budget within time and keep budget track for closer.
- Prepare the rough draft of Revenue and Capex Budget with the help of Production team.
- Responsible to create: Form B, CIR, EA, WBS request, PR etc.
- Responsible to ensure and meet BASF guidelines related to Procurement.
- Funds according to budget approval for plant Process Improvement only.
-
Improvement & Project Control:
- Support to allocate resources to manage plant improvement activities & projects to ensure they are carried out as planned.
- Positive outcome so that plant performance will increase.
- Create an idea for productivity increase by way of digital solution and technical solution.
Plant Responsibilities:
- Support Manager toward “Increase Production Volume without compromising quality of material and safety, Reduce Scrap and Rework”.
- Update the records by effective production planning, reduce product changeover time, prompt rectification and update SAP and GAP entries on product quality deviation during production.
- Ensure to update SAP; GAP and Other BASF system tools report updating on daily basis.
- Sustain good Health of equipment's by preventive maintenance with teamwork.
- Timely production of qualitative products.
- Help Manager for arranging training and Team Performance activities.
- Safety implementation and its simulation at shop floor.
- OAE Improvements and update Monthly reports.
- Help Manager to arrange Operator, Engineer, and Supervisor’s training.
- Responsible for daily production indicators, Including quality indicators and cost controls.
- Participate in quality initiatives, Control Product quality standards and purpose corrective measures when necessary.
- Plan production on weekly and daily basis and ensure to have availability of all necessary resources. Monitoring the production KPIs and Production Scheduling and take necessary
- Operational decisions in case of deviation.
- Perform product test and adapt production parameters if needed. Ensure the daily production reporting.
- Help to Plan, together with Maintenance, the daily, weekly & Monthly maintenance.
- Conduct and lead daily Operation meeting with Maintenance and Production team in absence of Production Manager.
- Supervise day-to-day maintenance work, Performed by operators and report to Manager in case of abnormality.
- Ensure daily inspection of plant for any deviation as per RC requirement and report to Manager.
- Execute and help to supervise shutdown (Turnaround) and ensure the safety of the installation.
- Contribute to the Manufacturing Excellence and Innovation Programs.
- Develop/Improve Production process Sequences according to plan.
- Help and implement and follow up the entity’s budget, objectives, policies and procedures.
- Communicate messages from the manager to the operators, and vice-versa.
Authorities (Deputation Rules):
- In absence of Production Engineer appoint deputy to take care of Production Engineer responsibilities.
- Production related activities responsible person is Manoj Vasava and Production Process related activities Process Engineer is responsible.
Deputy ‘Allowed to do’ in the absence of Production Head
- Shall take decisions in plant to ensure effective implementation of RC
- Shall ensure proper utilization of resources for effective implementation of RC
- Shall communicate the department Head in case incidents if any
- Shall take mitigation measures, in emergency as per on site emergency plan.
- Shall consult the Production Head or Site Head for taking any emergency shutdown of the plant / process
- In case of Process / Quality variation shall analyze the root cause and then take the decision to override the interlocks, if required, and then communicate the same to the Production Head
- Shall take decision on interlock bypass with consultation of the Production Head & EHS Head
- Shall sign work permits as per work permit matrix.
- Deputy ‘Not Allowed to do’ in the absence of Production Engineer
- Shall not take any decisions on Statutory issue and organization change.
- Shall not take any decisions pertaining to RC policies.
- Shall not deviate from RC procedures and permit to work system.
- Shall not approve any RC procedures.
Key Activities:
- Maintain Production, Quality & Safety
- Smooth Plant operation
- Plant SAP related Documentation.
- Ensure to have Plant consumable items.
- 5S / House Keeping
Job Skills:
- Equipment Knowledge of production / packaging equipment, and knowledge of instrumentation / control system, and automation, including technical standards
- Process Unit Operations and Good knowledge of Documentation; SAP.
- Good Communication Skills.
Job Requirements
Education |
BSC / MSC / CIPET |
Working Experience |
05-10 Years |
Technical & Professional Knowledge |
Extrusion equipment; compounding process & Chemical Industries Exp. |
A unique total offer: you@BASF
At BASF you get more than just compensation. Our total offer includes a wide range of elements you need to be your best in every stage of your life. That’s what we call you@BASF. Click here to learn more.
A unique total offer: you@BASF
At BASF you get more than just compensation. Our total offer includes a wide range of elements you need to be your best in every stage of your life. That’s what we call you@BASF. Click here to learn more.
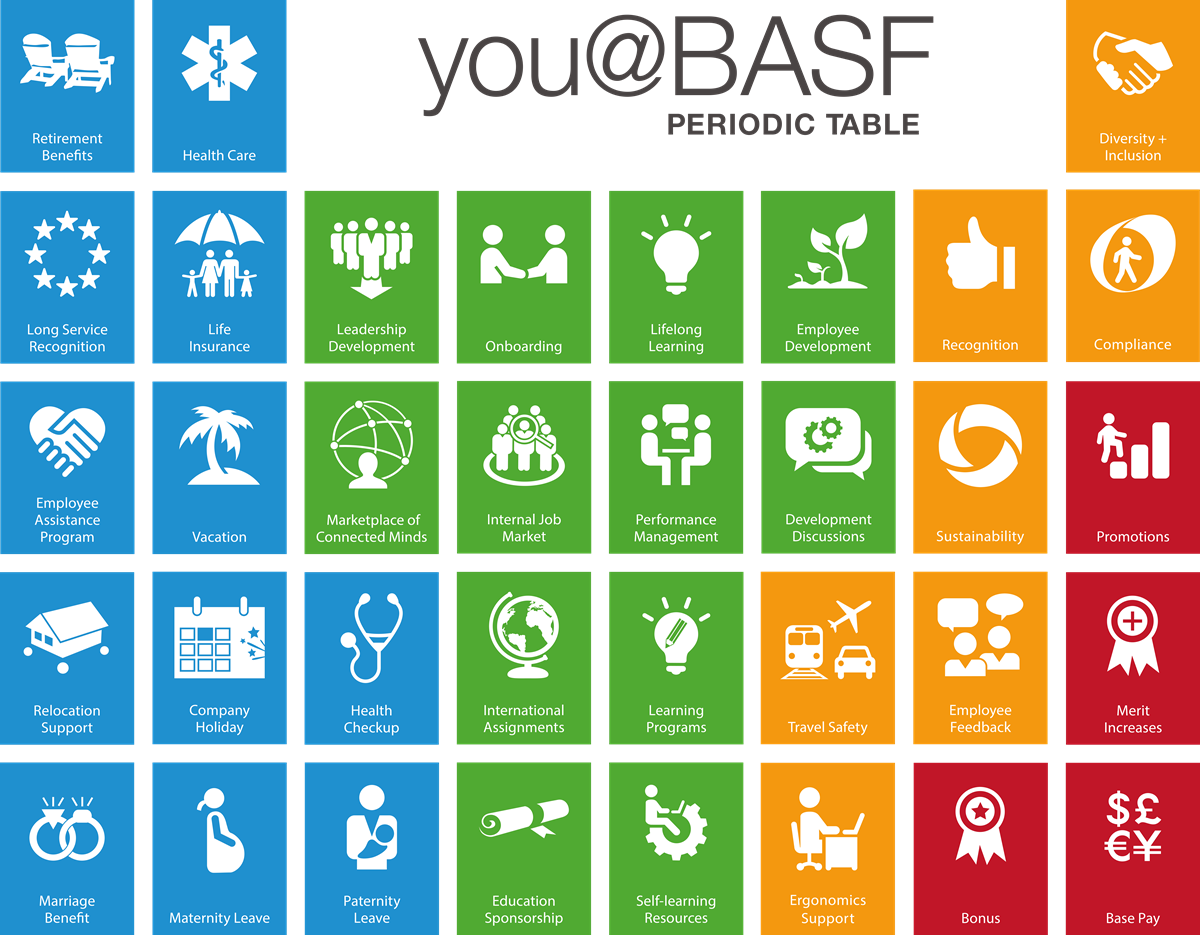
Working at BASF: We connect to create chemistry
We are proud of strong history of innovation, which has helped make us who we are today – the world's leading chemical company. Every day, our global team of over 120,000 individuals work together to turn visions for sustainable solutions into reality by connecting with one another and sharing our knowledge.
The right people are crucial for our sustainable success. We aim to form the best team by bringing together people with unique backgrounds, experiences and points of view. Our differences make us stronger and more vibrant. And an open, creative and supportive work environment inspires us to achieve exceptional results.
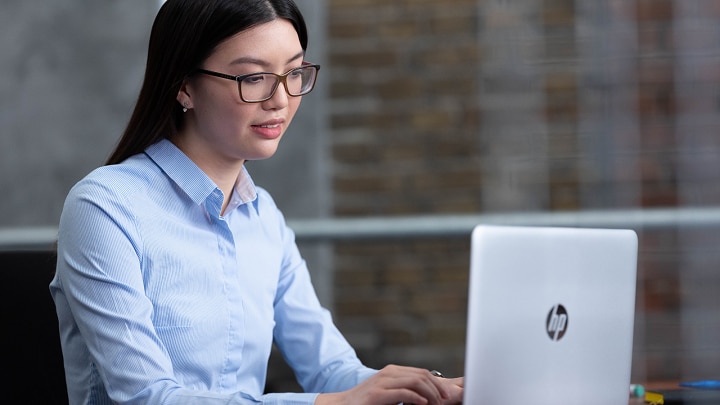
Your application
Here you find anything you need to know about your application and the application process.
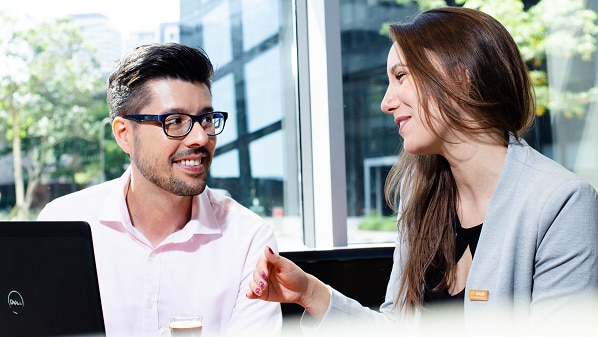
Contact us
You have questions about your application or on how to apply in Europe? The BASF Talent Acquisition Europe team is glad to assist you.
Please note that we do not return paper applications including folders. Please submit copies only and no original documents.
Panoli, GJ, IN, 393001